Integration of the Physical and Digital World
The future of industry is data-driven – but only if that data is seamlessly connected to the real world.
Making that connection work is the "digital twin"
- a perfect 1:1 representation of any physical system in the digital realm
- unlike a simple model, the digital twin is not static
- any change in the physical machine is immediately updated in its virtual counterpart and vice versa
- the totality of the physical and digital elements is a Cyber-Physical System (CPS)
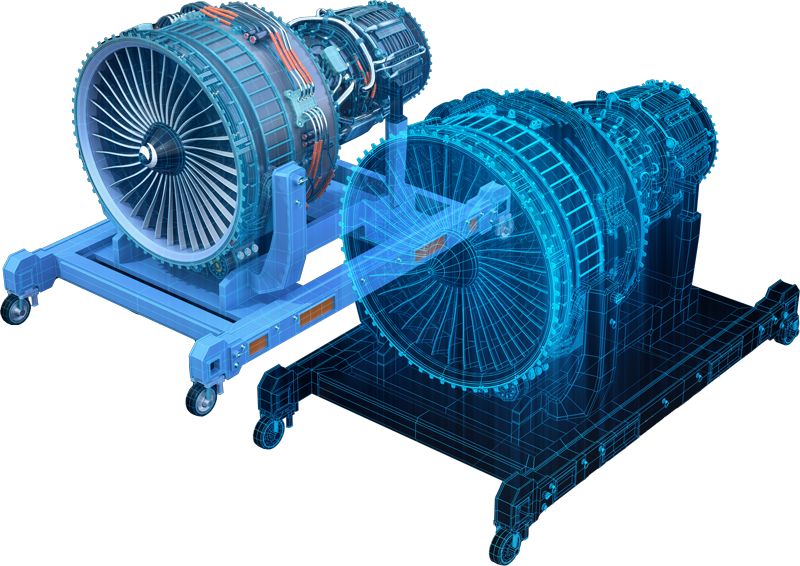
The Digital Twin Accompanies a Device Over Its Entire Lifecycle
Development
Say goodbye to costly prototypes. By designing and developing your system in a simulation environment, you can make changes in seconds. By developing software against the simulation model, programming and hardware design can now be done in parallel while simulated testing allows you to correct flaws in the model without expensive hardware changes. Iterations are much faster and your time to market is massively improved.
Engineering and Commissioning
Any machine builder or system integrator will tell you on-site assembly and commissioning is a major hassle. It can take weeks to tweak parameters to local circumstances. Even seemingly minor things like humidity or average temperature can have a major effect on precision machinery and necessitate appropriate fine tuning. By taking a survey of the customer site and feeding these values into your simulation, you can predict the necessary machine parameters by tuning your digital twin. Once you have the optimal settings figured out, local commissioning will be a breeze.
Operational Life Span
By keeping an eye on the digital twin’s data, anomalies are detected faster and can be fixed before any damage is done. Process optimizations can be tested in the simulation before applying them to the real world, avoiding costly trial and error. System changes and expansions are planned on the virtual device for enhanced safety and efficiency.