Prozessverbesserung durch zeitdeterministische Kontrollen
Jede Art von Verbesserung basiert auf Erfahrung – oft sogar auf „Trial and Error“. Aber im Bereich der industriellen Prozessqualität ist es viel zu kostspielig, sich auf Versuch und Irrtum zu verlassen. Der Weg zur Prozessverbesserung führt über die Analyse von Maschinen- und Produktionsdaten. Dazu werden in der Regel eine Vielzahl von Daten aufgezeichnet und zur Analyse an einen Cloud-Anbieter gesendet. Sobald die Ergebnisse vorliegen, können die Parameter für den nächsten Produktionslauf optimiert werden. Wenn es doch nur eine Möglichkeit gäbe, aktive Prozesse zu optimieren, während sie noch laufen…
Mit Xentara gibt es das jetzt.
Endlich wird der Regelkreis zwischen Maschine und IT geschlossen!
Bei Standard-IoT-Implementierungen fließen die Daten
nur „nach oben“:
- Aggregation von Daten
- Offline-Analyse
- Alarme, Berichte
- Dashboards
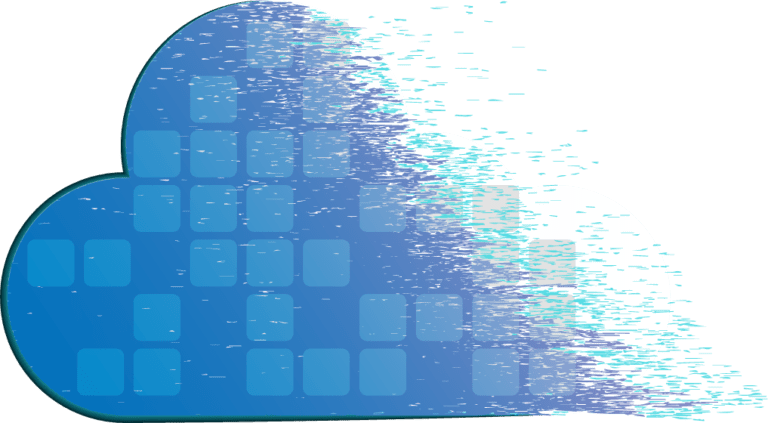
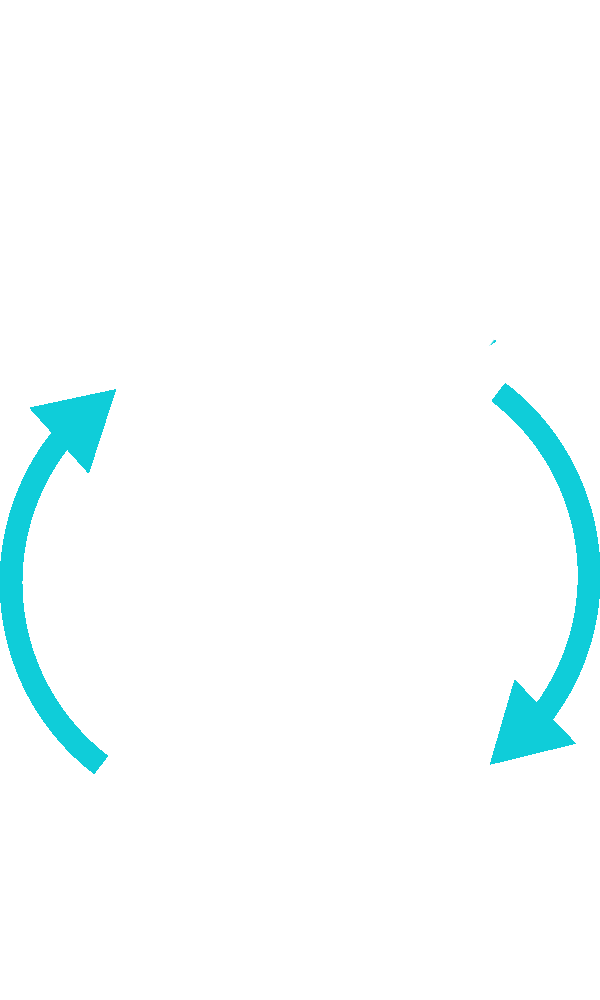
Mit der Xentara-
Plattform können Daten bidirektional fließen:
- Schließen des Regelkreises
- Aktion in Echtzeit
- Fortlaufende (Selbst-)Optimierung
- Intelligente Fertigung
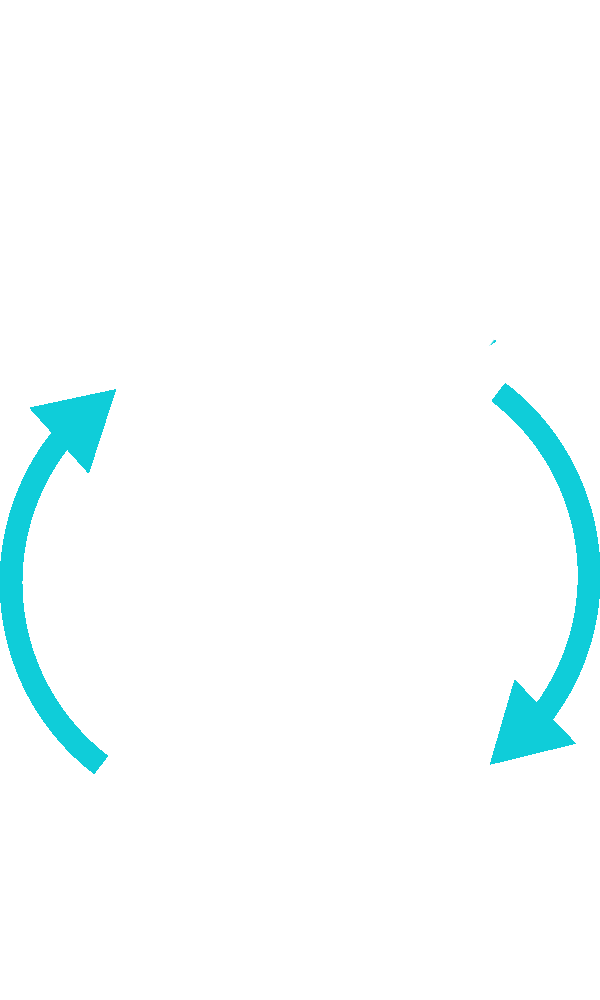
Der einzigartige, zum Patent angemeldete Echtzeit-Kern und das Timing-Modell von Xentara ermöglichen eine stabile, deterministische Kommunikation mit Maschinen – genau wie bei speicherprogrammierbaren Steuerungen nach Industriestandard – aber sogar noch leistungsfähiger als der Standard-SPS-Zyklus. Im Gegensatz zu SPSen, die nur einfache Steuerungslogik verstehen, kann Xentara jede IT-Technologie – wie Machine Learning – nutzen und nahtlos in den Regelkreis einbinden.
SPSen können nicht auf Änderungen reagieren, ohne neu programmiert zu werden. Durch den Einsatz von Xentara-basierten Edge Devices können alle Prozessparameter bei laufendem Betrieb angepasst und optimiert werden. Mit der intelligenten Anomalieerkennung werden abweichende Werte korrigiert, bevor sie ihren Toleranzbereich verlassen. Qualitätseinbußen werden rechtzeitig erkannt, um nicht eine ganze Produktionscharge zu beeinträchtigen. Verschleißerscheinungen werden genau überwacht, um eine vorausschauende Wartung zu ermöglichen, die anstehende Probleme behebt, bevor sie auftreten.
- bessere Produktionsausbeute und Qualität
- mehr Effizienz und Nachhaltigkeit
- bessere Haltbarkeit und Widerstandsfähigkeit der Geräte